Grow, harvest, clean, spin, weave, dye, design, sew and market. All these stages in the creation of clothes are largely outsourced to industrial processes that have cotton garments appear almost by magic for 21st century wearers buying on demand. JANE MILBURN reports.
About 90 percent of clothes bought in Australia are made overseas yet spinning is the only one of these processes that Australia can’t do right here, right now, today.
If we were to reintroduce onshore spinning capacity, this would enable local processing as well as recycling capacity to create a closed-loop fibre economy saving textiles from landfill.
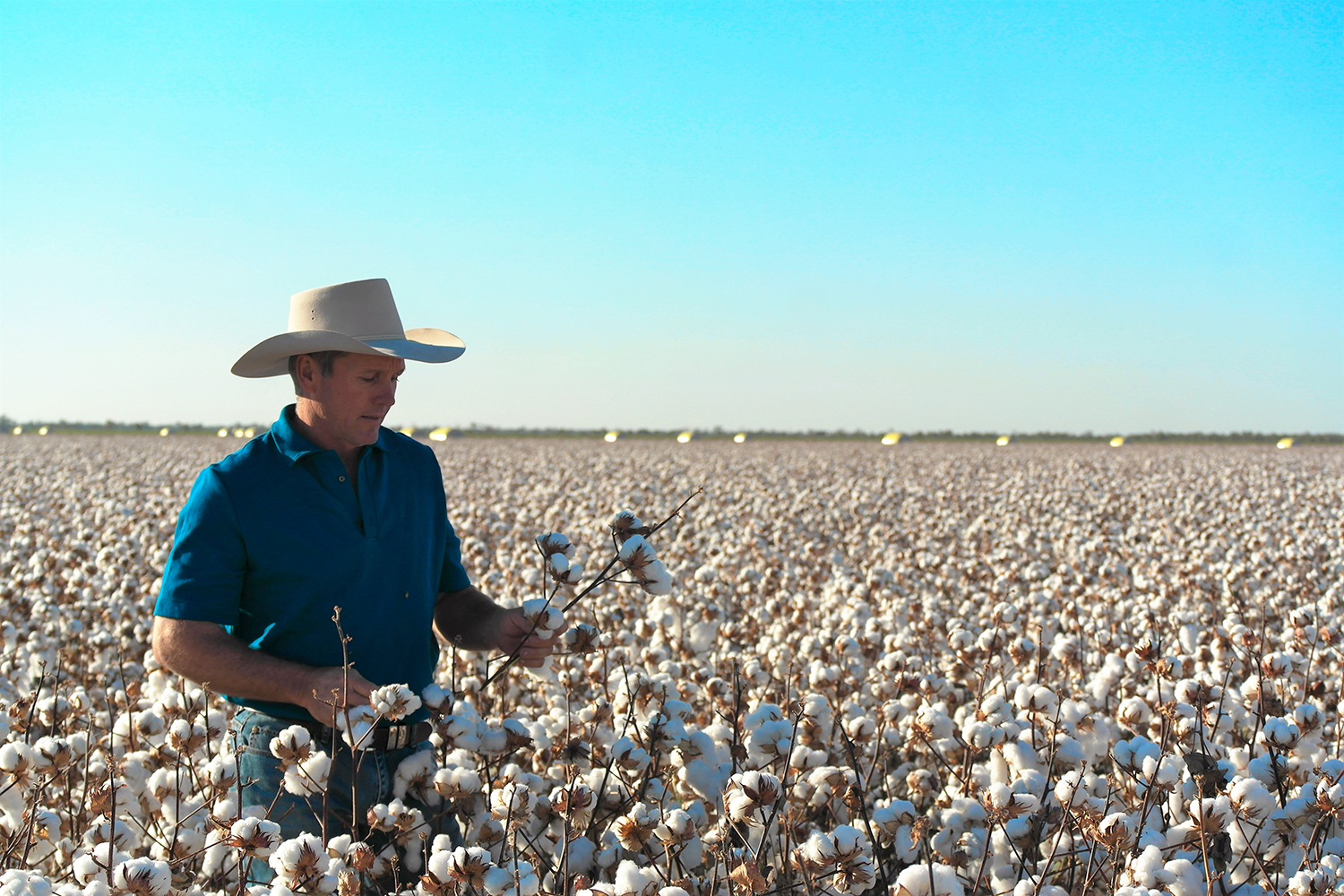
Glenn Rogan in his Australian Super Cotton field at St George.
Until recently, most wearers were not thinking about the missing stages of repair and recycle that can help make the journey of clothes more circular and reduce their ecological impact. Now we are asking more questions, taking actions and seeking solutions.
With increasing concerns about climate change and pollution, the circular economy is poised to grow and Australia needs to be part of it. Manufacturing has been migrating offshore for decades, but pandemic disruption of supply chains may herald a turning of the tide.
Cotton Australia CEO Adam Kay said advanced textile technology with automatic mills, new spinning techniques and renewable energy could reignite local fibre manufacturing within the next decade.
There is already a move away from China due to concerns about human rights abuses because Australian companies’ have formal obligations under the Modern Slavery Act 2018 in addition to moral and ethical considerations.
Governments want to bring manufacturing back onshore because the pandemic highlighted vulnerabilities in global supply chains, leading to the Australian Government’s Modern Manufacturing Strategy with the stated aim to manufacture a new future for our nation.
Australia is known for its raw materials, its wool and cotton, its iron-ore and coal, when it could be known for its textiles and steel if we now grasped the nettle and reinvested in manufacturing with green energy and technological innovation.
There is certainly impetus from the Australian fashion industry with a 2020 Reimagining local manufacturing report, by Alida Milani and colleagues Clare Miles and Sanna Conquest, noting shifts in consumer support towards more local and sustainable manufacturing.
Their interviews with fashion industry players revealed that COVID-19 has further highlighted the unsustainable nature of this industry on a global scale and exposed its weakest links. It affirmed that provenance and ethics are important for designers, manufacturers and consumers, and the potential to revive local manufacturing based on known origin and traceability.
The Reimagining local manufacturing report indicated the need for a 10-year plan from government, business and investors aligned with agricultural innovation, advanced manufacturing and a circular economy approach, as well as commitments to local procurement from government institutions, big brands and consumers.
Summarised quotes from the report include:
- Change has to come from the ground up, through a new lens of sustainability and resource efficiency towards a circular, regenerative model
- Onshore processing talks to our responsible sourcing of raw materials, we know where it is in the supply chain
- It’s incredible to think about the cost of baling all of the wool and cotton which gets shipped over and then it gets shipped back.
- We don’t have much legacy industry here so we can leap-frog to a circular system.
- There is a lack of infrastructure, no recycling stations, no end of life solutions. We need to fix the end, not just the beginning. We need to become self-sufficient.
- We need quick investment in high-end spinning machinery for our cotton and wool. From an origin of production perspective, you need yarn spun in Australia to export.
- We need farmers, producers, educators, industry leaders et al to come together to build a framework for the growth and longevity of the industry.
- The industry needs to be about connection, supporting local, and a high level of personalisation. It’s about building loyalty with customers, the opposite of fast fashion.
- We need to learn best practice globally and pull together a dream team of decision makers.
The report concludes Australia’s clothing and textiles industry needs urgent attention and COVID-19 presents a reset opportunity for better outcomes across multiple sectors.
After 40 years farming at St George, the Rogan family’s Australian Super Cotton enterprise is producing long-staple cotton for premium products and at the leading edge of change.
During the past 15 years, Glenn Rogan has noticed more consumer interest in provenance and ethical production and in the past 12 months a strong desire to support Australian industry.
Glenn is the grower behind Full Circle Fibres, the only Australian cotton supply chain albeit with the cotton shipped for spinning in Manchester, England, before returning home to be dyed, knitted or woven and turned into garments.
Based on all that has gone before, Glenn believes within three years there will be locally processed specialty Australian cotton available here because there are multi-layered benefits.
“Australian cotton growers are amongst the best growers in the world in terms of quality and yield, so why aren’t we processing it more in Australia? Commercial spinning is the missing link,” he said.
“From a family farming perspective, I know that every cotton or grain grower has a sense of pride in what they are producing and a genuine desire to see the end product. You put your soul into producing it, and it is natural to want to be part of the finished product. This is very difficult unless the manufacturing or processing is done locally.
“And whenever we export raw materials, someone else takes the profit. Cotton is a global commodity and we should be doing more locally so we realise more of the profit in Australia.”
Glenn believes small-scale high-end spinning in Australia can be achieved through collaboration between growers, knowledge about spinning processes and procurement certainty.
“We are further ahead than others because we have piloted with Meriel Chamberlin of Full Circle Fibres and brand owners, and we know what is possible. The next step is to bring spinning onshore. We need a line of finished products to underpin that and be able to offer manufacturers easier access to yarn without it having to go halfway across the world for spinning at short notice.
“We know technologically advanced spinning mills in Asia are fully automated and do ‘lights-out’ spinning that is managed hands-free. Yarn-testing experts and security are the only labour inputs once the buildings and infrastructure are in place.”
Glenn is not talking about spinning yarn for $5 t-shirts, rather high-end fashion and homewares, bedding and towels. This quality goes to the heart of sustainability because buying one or two quality items that last for years is more sustainable than many cheap throwaways.
Product miles matter too. As a consuming society, a lot of miles are put into the raw product to send it overseas and then back again to Australia. The energy and money that goes into moving things offshore and bringing them back could instead be invested in local manufacturing.
Glenn said genuine commitment by state and federal governments in the form of procurement of uniforms, and bedding and towels in hospitals, would ensure financial underpinning for a new industry that could deliver on many levels. Technology is available to ensure all the offcuts, as well as old sheets and towels, can be reprocessed as part of a circular manufacturing industry.
This article was first published in QCWA’s Ruth Magazine Winter 2021